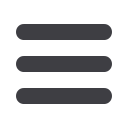
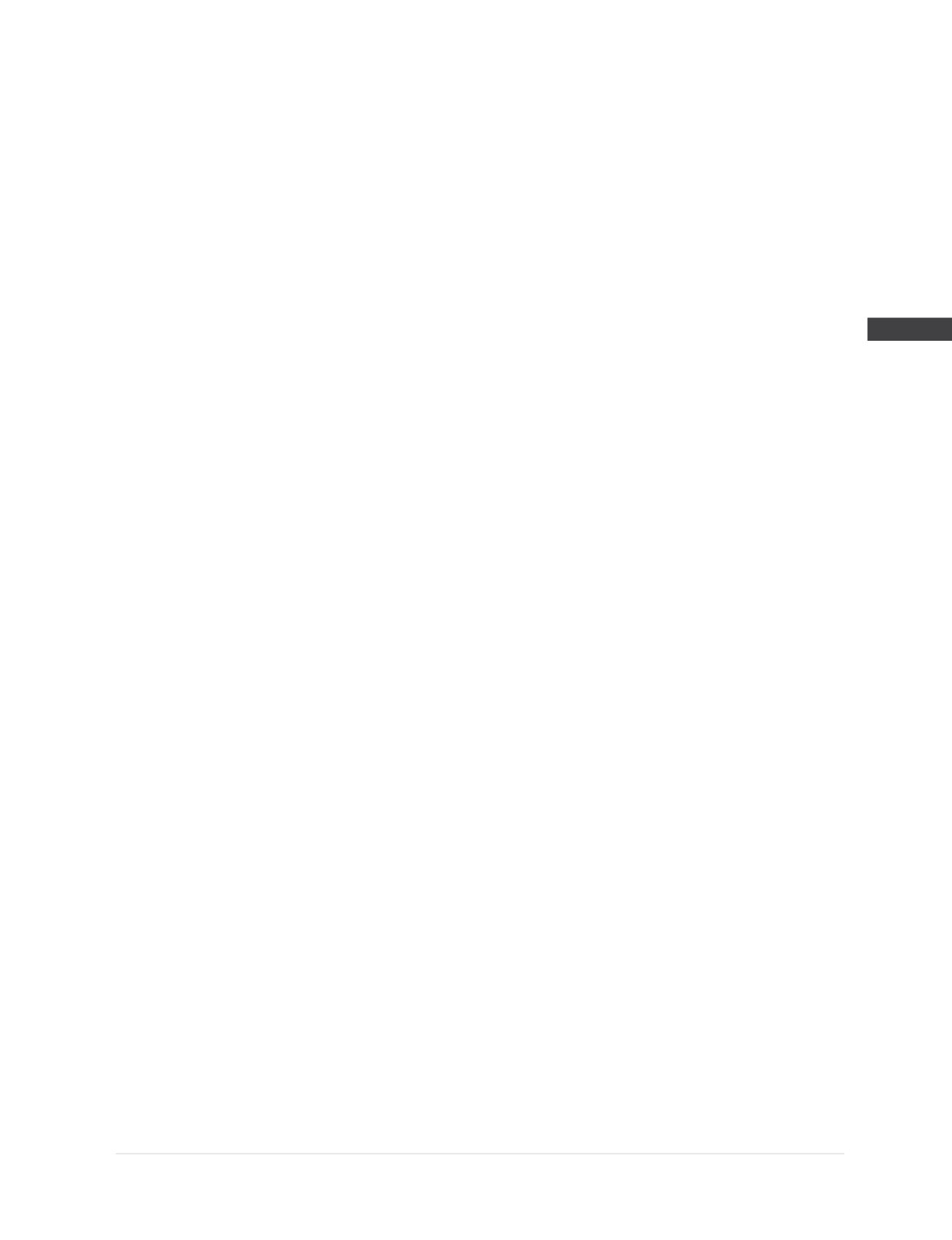
© 2014 Foundation Supportworks
®
,
Inc.
All Rights Reserved
p 201
APPENDIX 2G
GUIDELINES AND RECOMMENDATIONS
Chapter 2
Helical Foundation Systems
shall further note depths and magnitudes of high torque/pressure spikes, apparent encounters
with obstructions, or any other difficulties in advancing the helical piles.
4. Test piles/anchors and reaction piles shall be installed as close to vertical and plumb as possible,
unless battered or angled elements will be tested. Maintain installation speed under 25 rpm
during installation of the test and reaction piles. Installation speed should be further reduced
to 10 rpm or less for the final three to five feet of installation or when there is a risk of abruptly
exceeding the torque rating of the helical shaft.
5. The test frame shall have an allowable structural capacity greater than the maximum test load.
The test frame reaction piles shall have a combined ultimate soil capacity at least two times the
anticipated maximum test load. The maximum test load shall be determined by multiplying the
design working load by the appropriate factor of safety. Ultimate soil capacities for reaction piles
are determined by multiplying the installation torque by the applicable default torque correlation.
6. The test frame shall be installed with the main beam centered over the test pile. The main beam
and the reaction beams shall be as close to horizontal (level) as possible and the reaction piles
shall be as close to vertical as possible.
7. Tests procedures should generally follow ASTM D1143 (Compression) and ASTM D3689 (Tension).
Criteria for evaluating the ultimate capacity of the pile is provided in AC358, Acceptance Criteria
for Helical Pile Systems and Devices, by the International Code Council Evaluation Service, Inc.
(ICC-ES). Alternative failure criteria may be proposed by the engineer of record. Such criteria
must be provided to FSI prior to installation of the test piles/anchors and reaction piles.
Load Test Communication and Responsibilities
1. A representative of the Engineer of Record or the Owner should be on site prior to initiation of the
load test and should remain through completion of the test cycles.
2. When an extended or long term test is required, procedures and data recording should be detailed
by the Engineer of Record.
3. The Engineer of Record, the Owner, or the Owner’s Representative shall have the opportunity to
physically read dial gauges and record measurements.
4. Engineer of record and FSI engineering shall be provided with a copy of the proposed test pile/
anchor installation procedures and load test procedures for review and comment prior to the start
of any site work.
FSI Travel and Expenses
1. FSI has a vested interest in the success of all FSI installing contractor load test operations and
offers field assistance when necessary to support its contractor network. FSI typically requires
the FSI installing contractor to pay travel costs and expenses for FSI representatives to travel to
the project site to provide support. In special cases, FSI may choose to assume some or all of the
travel costs and expenses for the FSI representative to be on site for the load test. In the event
that the FSI installing contractor fails to be prepared to a reasonable degree and this contributes
to extensive delays and extended or repeat trips, FSI reserves the right to pass unnecessary
costs on to the FSI installing contractor. Proper communication and organization should prevent
additional costs that are within control.