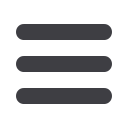
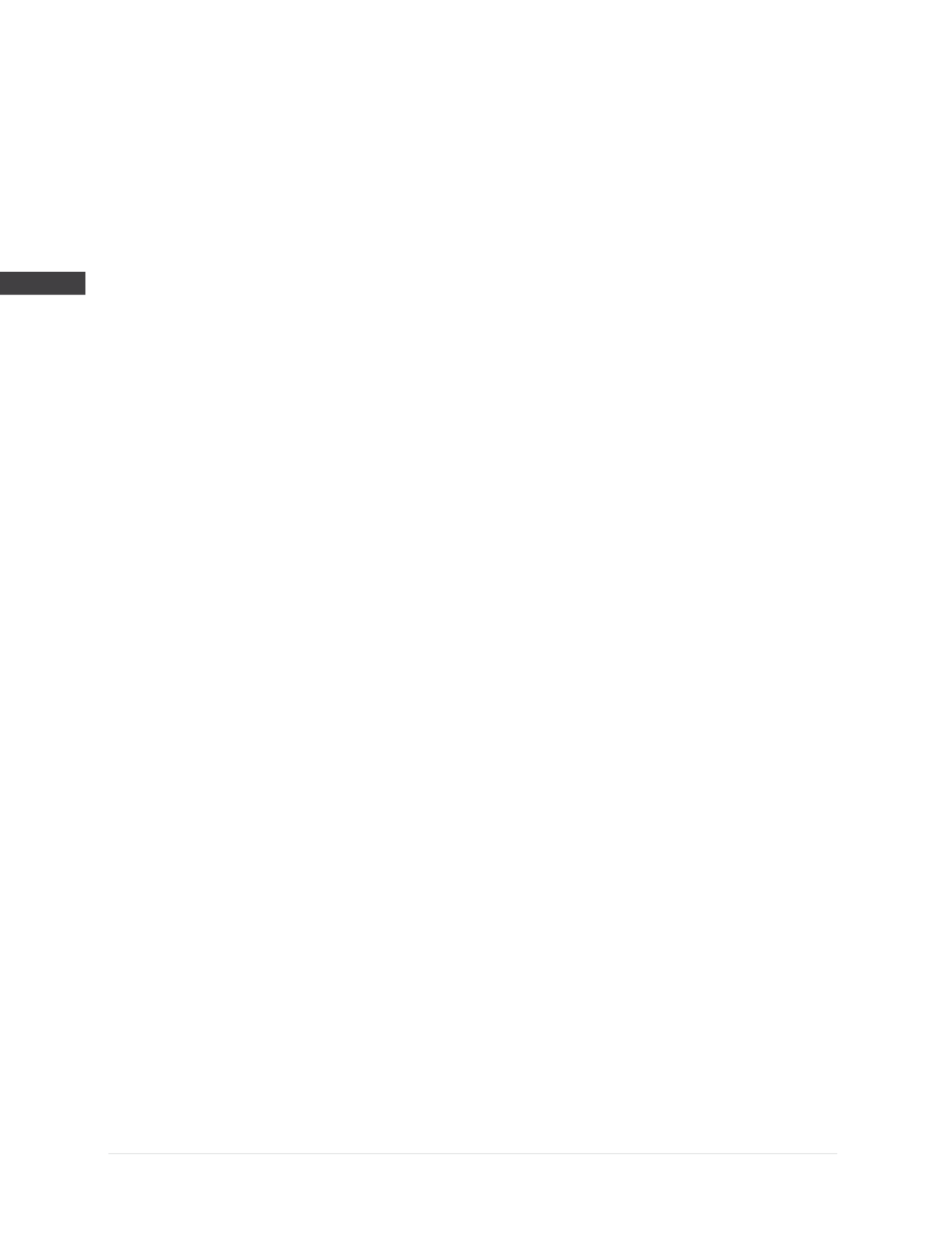
© 2014 Foundation Supportworks
®
,
Inc.
All Rights Reserved
p 132
APPENDIX 2E
CORROSION CONSIDERATIONS
Chapter 2
Helical Foundation Systems
(leads, extensions and bracket assemblies) are
available hot-dip galvanized in accordance with:
• ASTM A123, Standard Specification for Zinc
(Hot-Dip Galvanized) Coatings on Iron and
Steel Products
Hardware and fasteners may be hot-dip
galvanized, electro-plated, or mechanically
galvanized in accordance with:
• ASTM A153, Standard Specification for Zinc
Coating (Hot-Dip) on Iron and Steel Hardware
• ASTM B633, Standard Specification for
Electrodeposited Coatings of Zinc on Iron
and Steel
• ASTM B695, Standard Specification for
Coatings of Zinc Mechanically Deposited on
Iron and Steel
A Common Sense Discussion
Potential corrosion may be an objection for
specifiers considering helical piles. These
specifiers may feel that helical piles may not be
an appropriate option because of their concerns
about the steel corroding away and leaving
the supported structure on a compromised
foundation. While it’s true that steel does corrode
over time, it is actually quite rare that corrosion
will govern the design of new construction
helicals. This is because of the nature of how
helical piles are designed and installed. To state
it simply, the amount of steel which is required to
develop the necessary torque during installation
far exceeds the amount of steel that is required to
resist the design axial compressive forces. This
can be demonstrated in the following example.
A helical pile is required to resist an allowable
compressive load of 35 kips. The FSI Model
HP288 helical pile is selected for the project (see
Appendix 2A, Helical Product Ratings, Properties
and Details). The pile is installed to a torque
of 7,800 ft-lb to provide an ultimate torque-
correlated soil capacity of 70 kips (FOS = 2.0). The
pile has an uncorroded cross-sectional area of
the shaft of 2.11 in
2
and an allowable mechanical
axial capacity of 74.0 kips on the day the pile
is installed. However, the overall allowable pile
capacity would remain at 35 kips, limited by the
installation torque and the correlated allowable
soil capacity, even though the steel section in the
ground is capable of a great deal more.
Following installation, we can now consider the
effects of corrosion. ICC-ES AC358 provides
scheduled losses or “sacrificial thicknesses” for
black steel or steel with protective coatings, and
these sacrificial thicknesses must be considered
for design purposes. These sacrificial thicknesses
are based on moderately corrosive soils over a
period of 50 years. This is a design criteria only
and should not be confused with service life.
In our example, after 50 years in the ground, a
black, uncoated steel pile would have lost a steel
thickness of 0.036 inch due to corrosion. The pile
would have a remaining cross-sectional area of
the shaft of 1.82 in
2
and an allowable (mechanical)
axial capacity of 63.6 kips. This is the value that
Foundation Supportworks lists as the “plain
corroded” allowable mechanical axial capacity in
compression for the HP288. The overall allowable
pile capacity still remains 35 kips, limited by the
installation torque that was applied 50 years earlier.
So how much steel would have to be lost before
corrosion would begin to govern the design? See
Figure 2E.1
. The remaining allowable mechanical
capacity does not fall below the allowable pile
capacity of 35 kips from our example until the
sacrificial thickness reaches 0.135 inch. This is
nearly four times greater than the scheduled 50-
year corrosion loss rate for black steel and over
eight times greater than the scheduled 50-year
corrosion loss rate for hot-dip galvanized steel.
Corrosion is a very complex subject involving
many factors which can affect loss rates.
With some understanding, it quickly becomes
apparent that even if the corrosive properties
of the soil at a particular site are especially
aggressive, it is still quite rare for corrosion to
govern the design of a helical pile solution.