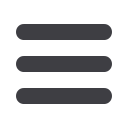
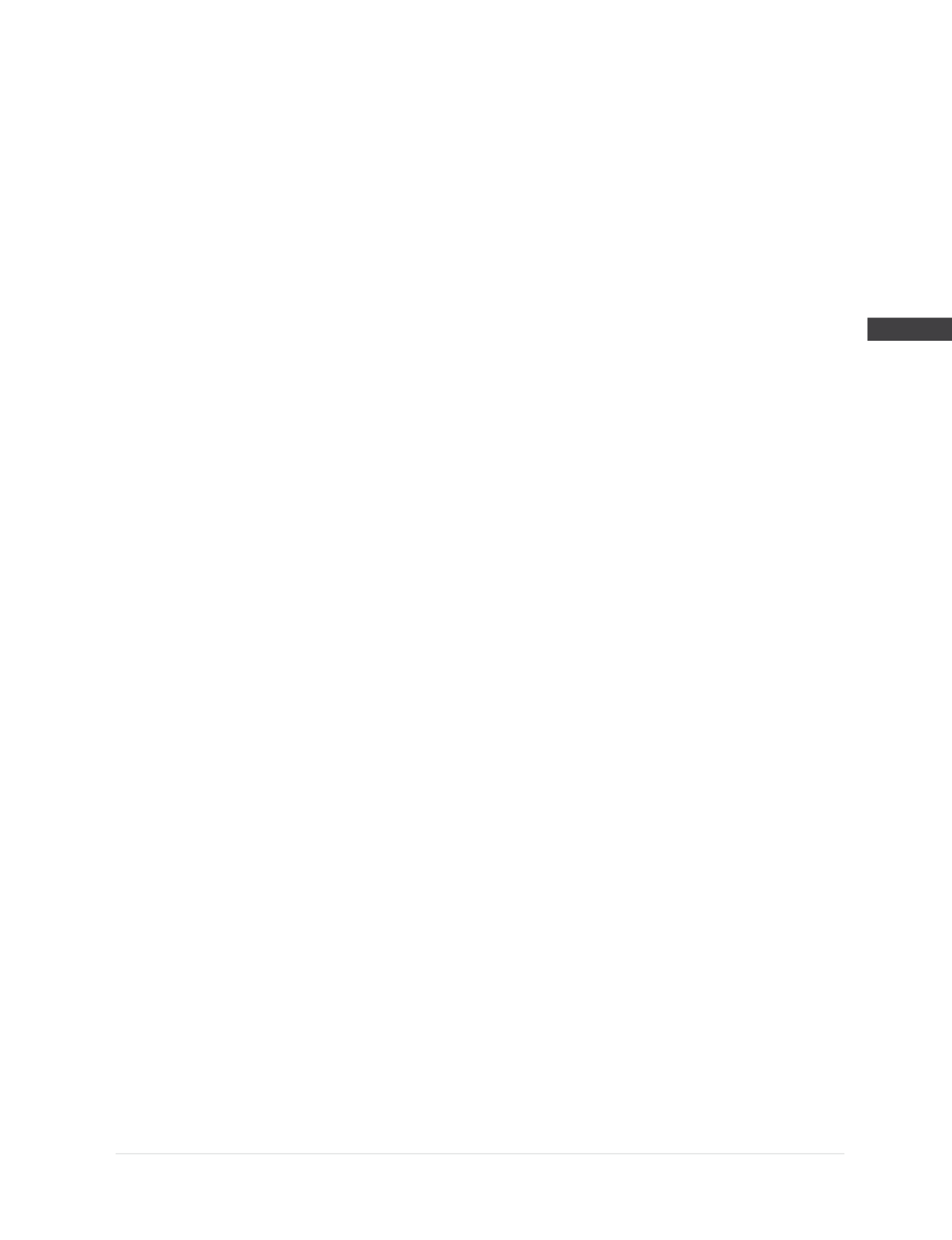
© 2014 Foundation Supportworks
®
,
Inc.
All Rights Reserved
p 193
APPENDIX 2G
GUIDELINES AND RECOMMENDATIONS
Chapter 2
Helical Foundation Systems
1. Establish a relationship with a local geotechnical engineering firm. An established, local
geotechnical firm may have performed a previous investigation within the area of the proposed
project, or have knowledge of the general soil profile. A discussion with the geotechnical firm
would allow the installing contractor to, at a minimum, determine if soil conditions are suitable
for use of helical piles or push piers.
2. Contact local well drilling firms for any information regarding local ground/geologic conditions.
3. Contact the Geologic Survey for the applicable State jurisdiction. This agency often maintains
records of test borings and wells throughout a given state, and this information may be used to
support a preliminary design effort.
4. Conduct a test installation of a helical pile/anchor, also called a “helical test probe”. A typical helical
test probe consists of a Model HA150 or Model HA175 lead section with a single 10 or 12-inch
helix plate and multiple extensions to reach the required depth. For some soil profiles, a double
helix may be necessary to provide the thrust needed to penetrate stiff or dense strata or advance
through particularly soft zones. For these situations, a double 8/10 or 10/12 helix configuration
generally works well. Torque must be monitored in one foot intervals during installation of the
test probe(s) from the ground surface to the termination depth. The torque readings must be
taken with calibrated equipment such as a certified gear motor and calibrated pressure gages or
by using a calibrated torque transducer in line with the drive tooling. The depth of investigation
would be similar to that described above; i.e., 5 to 10 feet below the anticipated depth of the
production piles. A general understanding of the soil profile and depth to groundwater may be
required to back-calculate soil strength from a helical test probe. The proposed number of helical
test probes for a given project is dependent upon the project characteristics and the variability
of site soil conditions. Factors of safety greater than 2.0 must be considered when the helical
pile/anchor design is based solely or in large part on the results of helical test probes. The
following information is required when evaluating the results of helical test probes: make and
model of the gear motor, calibrated torque readings, test probe shaft size, and test probe helix
plate configuration. For push pier projects, the installation of a test push pier typically provides
sufficient information for a push pier preliminary design.
5. Performa load test. If site access allows the setup of a load test frame, the results fromcompression
or tension load tests can determine helical pile or anchor capacity without soil information. The
required number of load tests would again be dependent upon project characteristics and should
be determined by design professionals. The helical piles or anchors used for the load test(s) shall
be installed with calibrated equipment so the true installation torque is known. The load tests
should be performed in general accordance with applicable ASTM standards. A site-specific
torque correlation factor can be determined from the results of the load test(s), which would then
allow the final installation torque readings to be used for pile capacity verification.
Helical piles, helical anchors and hydraulically-driven push piers are installed routinely on residential
projects without adequate site-specific soil information available. The homeowner is often unwilling
to pay for deep soil borings, laboratory tests and recommendations from a geotechnical consultant.
In these cases, the installing contractor typically proposes a specific pile or anchor system with
depth/length and product spacing based upon experience from doing previous work in the area. The
contractor then follows rules-of-thumb guidelines for installation.
FSI offers a software tool called “Foundation View” to assist FSI installing contractors in estimating
structural residential loads and spacing of retrofit piers. This program assumes that the soils are