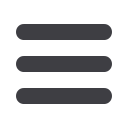
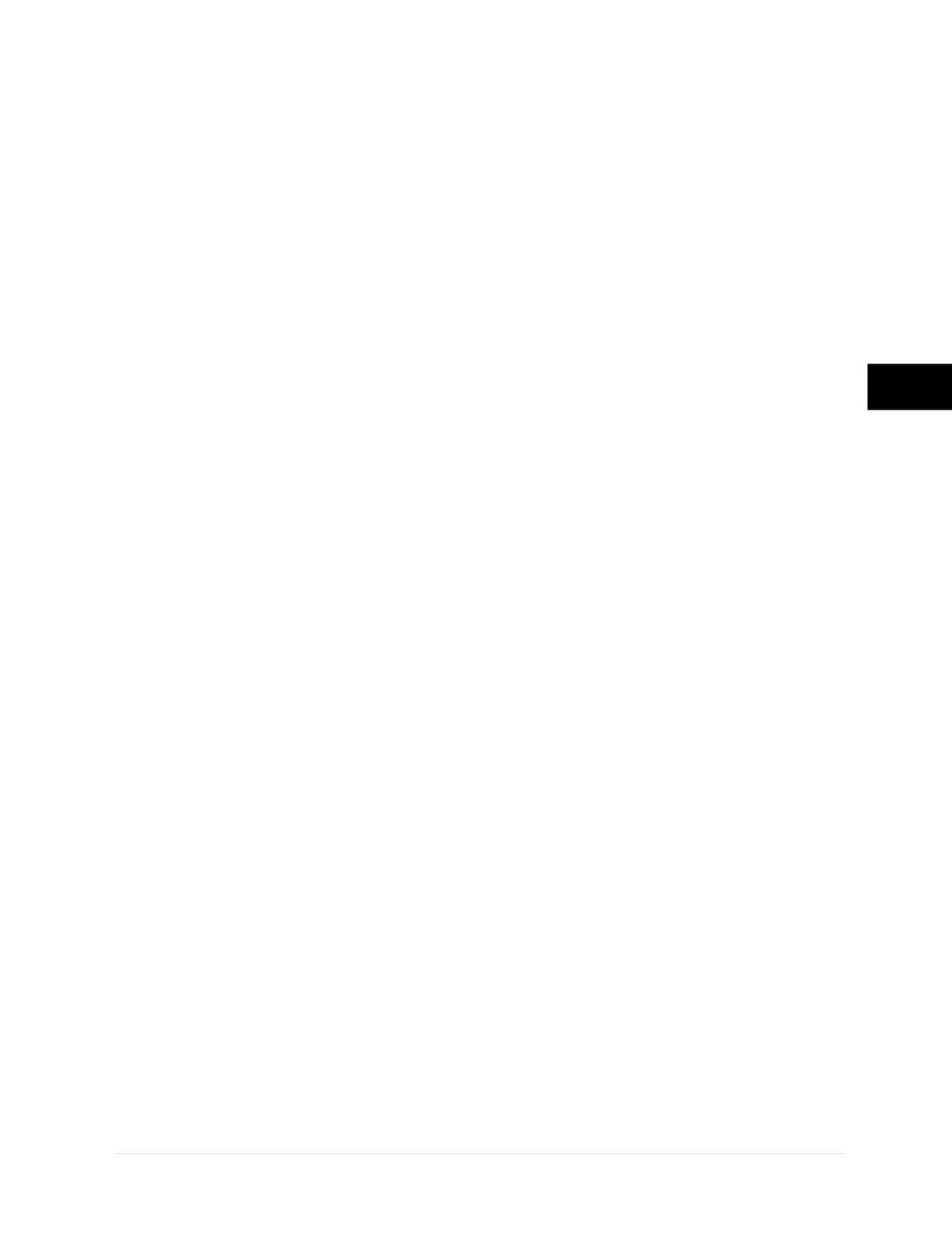
© 2014 Foundation Supportworks
®
,
Inc.
All Rights Reserved
p 225
Chapter 3
Hydraulically-Driven Push Piers
CHAPTER 3
HYDRAULICALLY-DRIVEN PUSH PIERS
Overall dimensions of a push pier cross section
are 4 inches or less in most applications.
These sections are therefore very sensitive to
the bending moments introduced by eccentric
loading. Additionally, as pier bending moments
increase, the pier axial capacity will decrease.
This loss of axial capacity due to the addition of
bending stresses can be demonstrated with the
following example. A given pier section with a
3.50-inch O.D., 0.300-inch wall thickness and a
yield strength of 35 ksi has a maximum allowable
compressive capacity of 59.3 kips according
to Allowable Stress Design. When a bending
moment of 40 kip-in is applied to the same
section, its allowable compressive capacity
drops to 24.7 kips. This is a reduction of nearly
60 percent of the section’s full axial capacity.
What’s more, this moment would equate to
an equivalent eccentricity of only 1.62 inches,
which is a seemingly small eccentricity and is
still within the envelope of a typical pier cross
section. Since, eccentricities for under-footing
bracket systems are generally within the range
of 3 to 4 inches, the loss of axial capacity due
to the resulting bending moments is a significant
design consideration.
The bending moment created by eccentric
loading is dissipated by passive resistance
of the soil against the pier tube within the first
few feet of soil support, therefore, the bending
moment only needs to be considered for the pier
tubes directly below the bracket. One method of
providing the necessary bending resistance could
involve using larger diameter and/or thicker pier
tube sections for the entire length of the pier. The
larger/thicker pier sections would resist bending,
yet still have sufficient axial capacity in reserve.
Although a seemingly reasonable approach, it is
not an economical one since the extra steel is
only useful within the region of bending for the
first few feet below the bracket where the bending
moment is dissipated into the surrounding soil.
Another method used by many manufacturers is
to utilize internal or external pier reinforcement
after the pier has been exposed to the final drive
force. Internal reinforcement is simply smaller
diameter pipe or tube sections set inside the
pier and generally spanning between the internal
couplers of the pier shaft. Internal reinforcement
can be of inconsistent length and not placed at
the optimal location; i.e., extending through and
below the bracket, since final coupler location
cannot be estimated or predetermined. Also,
internal reinforcement is not generally placed until
after the final drive load has been applied, when
the maximum bending moment may have already
caused the pier shaft to deform or buckle. There
is little chance for success when trying to insert a
straight pipe section through a bent tube. External
reinforcement typically consists of larger round or
square hollow sections driven or placed around
the pier, again after the pier has been exposed
to the final drive force. Similar challenges exist
with placement of straight external reinforcement
elements over a bent pier.
Foundation Supportworks has developed
a unique approach to address the issue of
eccentric loading on retrofit push pier systems…
the external sleeve (see next section).
3.3.1.2 External Sleeve
The FSI PP237, PP288 and PP350 push pier
systems incorporate a 48-inch long external
sleeve to resist the bending forces generated
by the eccentric loading on the under-footing
and flush-mount brackets, thereby preserving
the axial capacity of the pier sections
(Figure
3.3.1.2.a)
. The external sleeve is hydraulically
driven with and around the pier starter tube
section to extend through and below the bracket.
The effect of the sleeve essentially creates
a bracket that is 48 inches tall without any
additional excavation. A 30-inch long external
sleeve is available for the PP237 and PP288
push pier systems for use in limited headroom
and crawl space applications.
The moment or bending force is localized within
a relatively short distance below the bracket.
Although the bending force is dissipated quickly
by the pier bearing against the confining soil,
it is significant and cannot be ignored. The