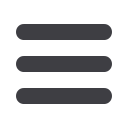
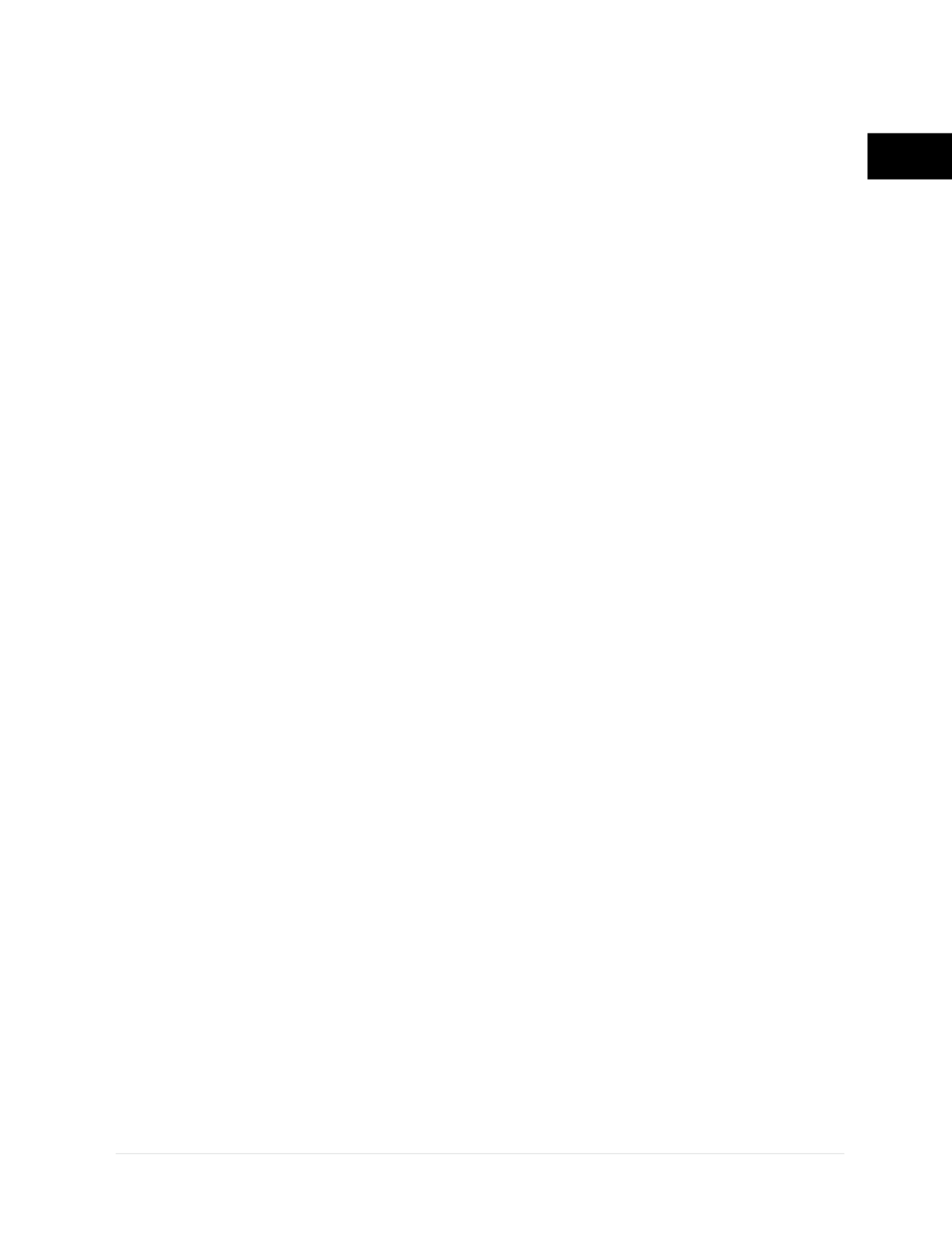
© 2014 Foundation Supportworks
®
,
Inc.
All Rights Reserved
p 27
Chapter 2
Helical Foundation Systems
CHAPTER 2
HELICAL FOUNDATION SYSTEMS
2.7.3 Torque
Correlation Method
The torque correlation method has become a
well-documented and accepted method for
estimating or verifying helical pile capacity
during installation. In simple terms, the
torsional resistance generated during helical
pile installation is a measure of soil undrained
shear strength and can be related to the bearing
capacity of the pile with the following equation:
Q
u
= K
t
x T
Where,
Q
u
= Ultimate Pile Capacity (lb)
K
t
= Empirical Torque Correlation Factor (ft
-1
)
T
= Final Installation Torque (ft-lb)
The relationship between installation torque and
helical pile capacity was generally considered
proprietary information by helical foundation
manufacturers until the results of an extensive
study performed by Hoyt and Clemence were
released in the late 1980s (Hoyt and Clemence
1989). The Hoyt and Clemence study included
tension load test results for 91 multi-helix piles
at 24 different sites with varying soil conditions,
embedment depths, shaft sizes, helix spacings
and number of helices. The helix plate spacing
along the pile shafts varied from 1.5D to 4.5D
and the number of helices varied from two to 14
with the diameters ranging from 6 to 20 inches.
Shaft sizes consisted of 1.5, 1.75 and 2.0-inch
square and 3.5 and 8.625-inch round. The
load test results were compared with capacity
predictions using the torque correlation method,
the individual bearing method and the cylindrical
shear method (Mitsch and Clemence 1985). The
statistical results of this study show that the
torque correlation method is the more precise
predictor of capacity of the three methods. The
researchers recommended torque correlation
factors (K
t
) of 10 ft
-1
for all size square bar shafts
and round shafts less than 3.5 inches in diameter,
K
t
of 7 ft
-1
for 3.5-inch diameter round shafts and
K
t
of 3 ft
-1
for 8.625-inch diameter round shafts.
It must be recognized that the recommended
K
t
values in the Hoyt and Clemence paper were
based on a wide range of soil conditions and
pile configurations (configurations that may
not be considered as conforming products per
ICC-ES AC358) and should only be used with
confirmation from site-specific, full-scale load
testing. Some of the recommended Hoyt and
Clemence K
t
values differ from the default values
provided in ICC-ES AC358.
ICC-ES AC358 recognizes the following
helical pile shaft sizes and default K
t
factors
for conforming systems, since the installation
torque to capacity ratios have been established
with documented research:
• 1.5 and 1.75-inch solid square K
t
= 10 ft
-1
• 2.875-inch O.D. round
K
t
= 9 ft
-1
• 3.0-inch O.D. round
K
t
= 8 ft
-1
• 3.5-inch O.D. round
K
t
= 7 ft
-1
The K
t
factors above may be considered
conservative for most applications, and even
though they are often presented as constants,
K
t
can vary depending upon the soil conditions.
K
t
factors are generally higher in sands, gravels
and overconsolidated clays, and lower in
underconsolidated clays, normally consolidated
clays and sensitive clays and silts. K
t
is also
inversely proportional to the shaft dimension/
diameter as shown above.
Factors that affect installation torque may also
have an effect on the resultant K
t
determined
from a field load test. In addition to soil type
and shaft dimension, studies have indicated
that other factors such as the number of helix
plates, helix thickness, helix pitch, helix spacing
along the shaft, helix diameter, depth of pile
embedment, applied downward force during
installation (crowd), and test load direction may
have an effect on installation torque and/or the
resultant K
t
. Other studies have discounted some
or most of these factors as inconsequential.
The use of uncalibrated torque monitoring
equipment or uncertified gear motors will likely