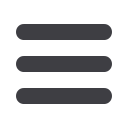
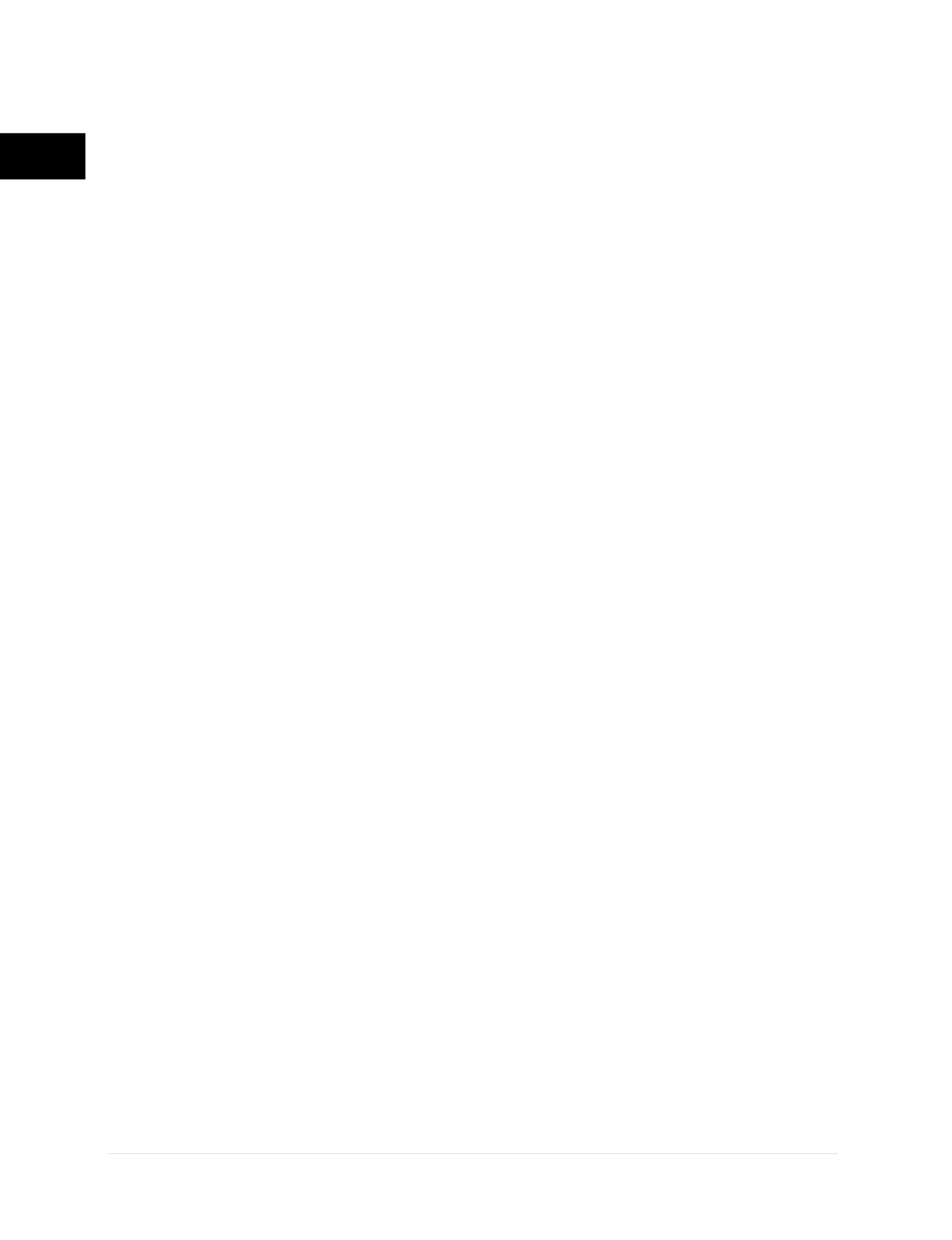
© 2014 Foundation Supportworks
®
,
Inc.
All Rights Reserved
p 18
Chapter 2
Helical Foundation Systems
CHAPTER 2
HELICAL FOUNDATION SYSTEMS
•
Vibration-free installation
– Rotary installation
of helical piles does not produce ground
vibrations, unlike traditional driven piles or
rammed aggregate soil improvement options.
•
Install quickly without generating spoils
–
Helical piles do not auger soils to the surface.
Therefore, there are no hauling or disposal
costs for spoils similar to auger-cast piles or
drilled shafts. For contaminated sites, disposal
and/or treatment of disturbed material can be
extremely costly or make the project cost-
prohibitive. Helical piles simply pass through
contaminated soils and do not bring them to
the surface.
•
Support of temporary structures
– Helical
piles can be removed from the ground by
reversing the installation process.
•
Load tests can be conducted immediately
following installation
– Installed steel piles
do not require a curing period like drilled
shafts or auger-cast piles. It is common to
install a helical test pile and then test it later
that day or the very next day. However, know
that especially on clay sites or clayey sand
sites, the soils will “heal” or “set up” around
the shaft and helix plates over time. In general,
within practical hold periods allowed by
construction schedules, the longer the pile sits
before testing, the higher the pile capacity for
a given amount of deflection.
•
Foundation concrete can be poured
immediately following installation
– Installed
steel piles do not require a curing period
like drilled shafts or auger-cast piles. On
schedule-sensitive projects, the contractor
may place reinforcing steel and pour
foundation concrete directly behind the helical
pile installation.
•
Clean installation
– Installation of helical
piles, helical tie-backs and helical soil-nails
does not include concrete or grout, thereby
minimizing equipment, vehicles and mess on
the construction site.
2.5 Limitations
Helical piles will not be the best-suited, most
economical deep foundation option for every
project or soil profile. In the same way, other
deep foundation alternatives such as driven
piles, auger-cast piles, drilled shafts, and drilled
and grouted micropiles, have their own benefits
and limitations and may be more or less suited
for certain project conditions.
• Helical piles are a steel foundation that will
be exposed to the atmosphere or buried
within the earth. AC358 defines corrosive soil
environments by: (1) soil resistivity less than
1,000 ohm-cm; (2) soil pH less than 5.5; (3)
soils with high organic content; (4) soil sulfate
concentrations greater than 1,000 ppm; (5)
soils located in landfills, or (6) soil containing
mine waste. In such environments, the steel
can be protected with a hot-dip galvanized
zinc coating or with other measures such as
sacrificial anodes. A site-specific evaluation
of the soil can be conducted in order to
determine an appropriate level of protection.
Refer to Appendix 2E for additional information
about corrosion.
• AC358 is currently limited to use of helical
foundation systems and devices supporting
structures in IBC Seismic Design Categories A,
B, or C, or UBC Seismic Zones 0, 1, or 2. Even
so, helical piles have been used successfully
across North America for decades and in
regions considered seismically active.
• Helical piles will not easily penetrate
construction debris, wood, dense gravelly
soils, or soils containing large, hard fractions
such as cobbles and boulders. These
materials could hinder installation or cause
damage to the helical pile shaft or helix plates.
When such conditions exist, a thicker or larger
pile shaft may be considered to resist impact
loading and torque spikes. Thicker helix plates
with a V-style cut could more easily penetrate
dense soils and, again, resist impact loading.
A solid square bar “stinger” lead section
coupled immediately to round shaft extensions