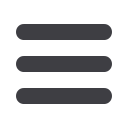
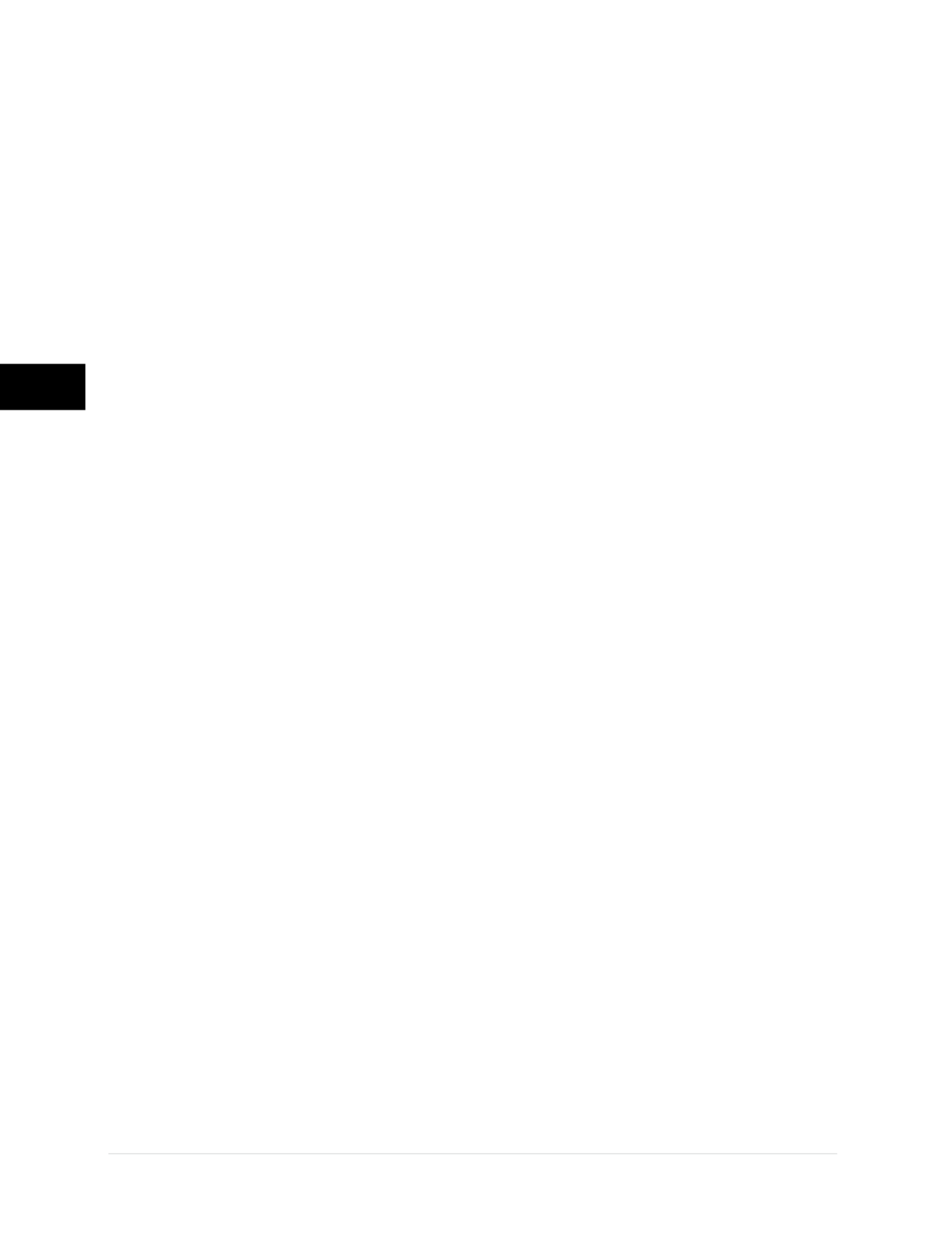
© 2014 Foundation Supportworks
®
,
Inc.
All Rights Reserved
p 234
Chapter 3
Hydraulically-Driven Push Piers
CHAPTER 3
HYDRAULICALLY-DRIVEN PUSH PIERS
3.9 Push Pier
Capacity and Spacing
Foundation Supportworks offers multiple pier
sizes and bracket assembly combinations to
provide solutions for varying applications and
design loads. A main design consideration for
eccentrically-loadedretrofitsystemsisminimizing
bracket rotation. This is accomplished not only
by designing a stiffer pier system, but also by the
system’s interaction with the surrounding soil
and the structure. Sections 3.3.1.1 and 3.3.1.2
discuss the bending forces that are generated
by the eccentric loading condition and how
the FSI external sleeve resists the bending
force below the bracket. The near-surface soils
surrounding the bracket, the external sleeve and
the upper sections of pier tube therefore act to
resist and dissipate the bending. Finite element
analysis software was used to analyze how the
external sleeve and pier interact with various soil
types and strengths. The standard 48-inch long
external sleeve was thereby selected to provide
an efficient use of additional steel to resist most,
if not all, of the bending force when piers are
installed within somewhat typical near-surface
soil conditions; i.e., loose sands and medium
stiff clays, or stronger. Although laboratory
testing cannot exactly duplicate actual installed
field conditions with all possible soil types
and strengths, the results from the standard
test method utilized (ICC-ES AC406) generally
confirmed these calculated capacities.
Retrofit bracket testing in accordance with
AC406 also considers interaction of the bracket
with a concrete block of known compressive
strength (2,500 psi). Testing pier systems
against concrete is completely logical as it
includes concrete failure as a potential failure
mechanism of the “system”. Bracket testing
within a rigid steel frame does little to simulate
field behaviors and failure conditions, and these
capacities could rarely be duplicated in the field
without first buckling the pier and/or breaking
the concrete footing. FSI determines push pier
capacities by testing in general accordance with
AC406 and, as a result, our pier systems may
appear to be conservatively rated versus other
published system capacities. Even so, AC406 is
an appropriate test method for determining push
pier system capacities, and the only standard
currently available.
Push pier system ultimate capacities may
be limited by the ability of the structure and
surrounding soil to provide the necessary
reaction to drive the piers. Light structures
or structures with shallow footings may start
to mobilize before the target drive load is
achieved. In such cases, it may prove beneficial
to excavate small, shallow holes at the pier
locations, instead of a full excavation, to allow as
much soil load as practical to remain around and
beneath the footing. The soil load can contribute
significantly to “hold” a light structure down in
order to achieve target pressures/loads. When
a structure experiences early lift, the project
engineer should evaluate if the drive pressure/
load is adequate, if adjustments can be made
to the proposed piering plan, or if a change to
retrofit helical piers should be considered. Helical
piers are installed by the application of torque
with machines independent of the structure.
Helical piers are discussed in Chapter 2.
A structural assessment should be performed
prior to installation to determine if the existing
footing, stem wall or floor slab can resist the
estimated final drive force without structural
damage. Overstressing the concrete can be
prevented or at least minimized by following
proper techniques and best practices for footing
preparation and pier installation. The contractor
should carefully monitor the installation and
release the load at the first sign of foundation or
slab distress.
Stone or cobble foundations, brick foundations,
or foundations that are severely broken or
deteriorated may not be good candidates for
retrofit foundation piers. Foundations and slabs
must be able to span between pier locations for
the system to be effective. Pier locations and pier
spacing are often determined by the spanning