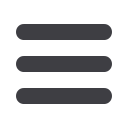
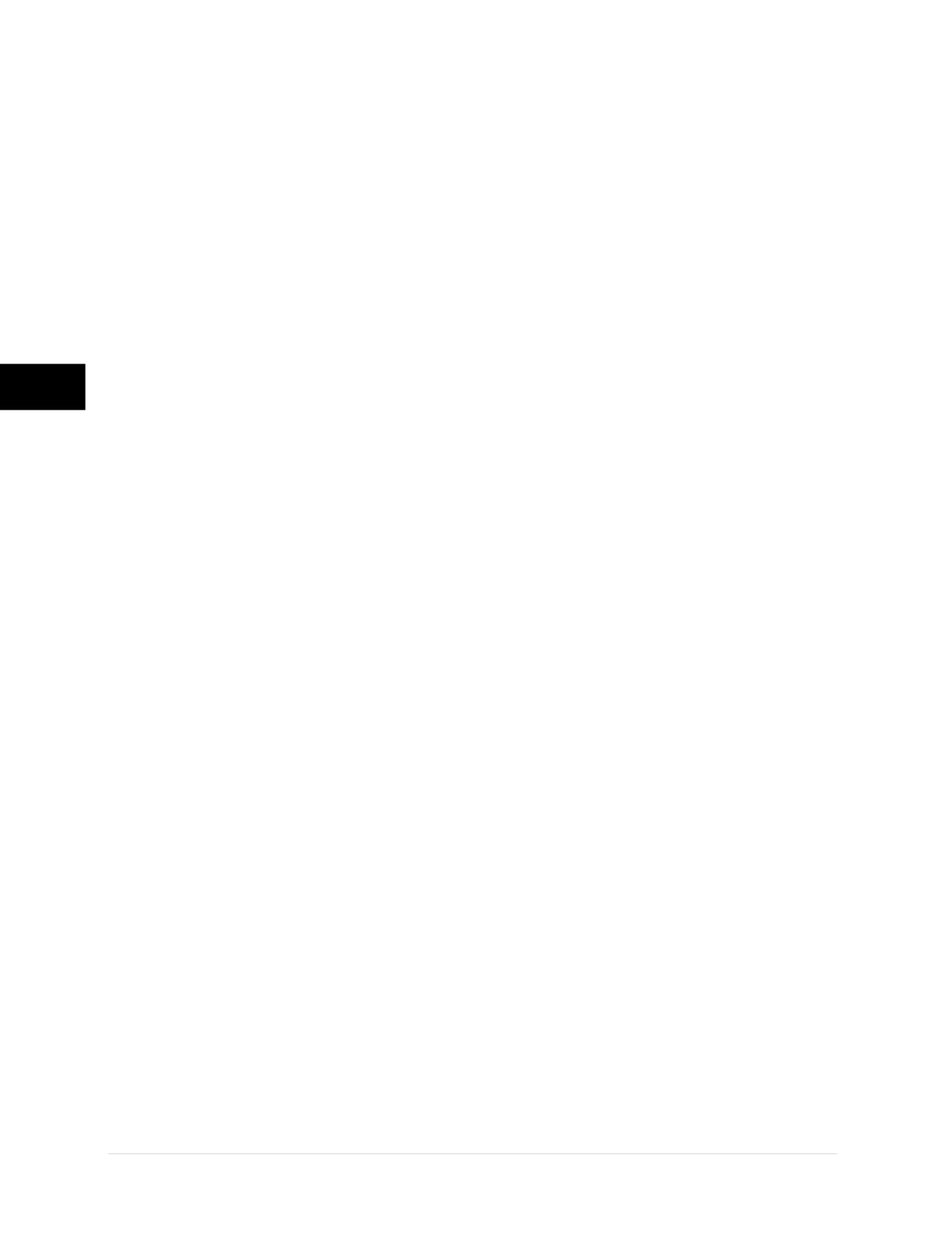
© 2014 Foundation Supportworks
®
,
Inc.
All Rights Reserved
p 236
Chapter 3
Hydraulically-Driven Push Piers
CHAPTER 3
HYDRAULICALLY-DRIVEN PUSH PIERS
loading and unloading procedure of driving
piers. At best, bolting provides little benefit to
the pier capacity and stability while introducing
the potential to weaken the system by damaging
the footing. Holes are included in the brackets
to be used at the discretion of the installer or if
a project engineer or building official requires
that the piering system be positively attached
to the structure.
Actually, the manner in which a push pier system
is loaded and supported would tend to cause the
bracket to push against the structure, not pull
away from it. At the same time, however, while
the bracket is pushing against the structure, it
also tends to rotate toward the structure. If the
pier system does not have adequate stiffness,
then the tendency for excessive bracket
rotation will be evidenced by the bearing plate
being pried away from beneath the structure.
This phenomenon does not mean that the
overall pier system is translating away from the
structure. Instead, it means the pier needs to
be much stiffer. The stiffness of FSI push pier
systems greatly reduces this rotational tendency
and precludes the need to positively attach
the bracket to the structure. When such an
attachment is made due to preference or local
requirements, FSI recommends the expansion or
adhesive anchors be installed after completion
of the piering operations. Anchors were not
used when the pier systems were tested in
accordance with AC406.
3.10 Under-footing
Push Pier Installation
The steps for under-footing push pier installation
include footing preparation, bracket mounting,
drive stand and drive cylinder attachment, pier
tube driving, application of the final drive force,
attachment of the lift cylinder assembly, structural
lift (if applicable) and load transfer and lock off.
Safety precautions must be followed prior
to and during excavation activities. Locate
underground utilities prior to excavation and
perform excavations at a distance away from
utilities as mandated by the utility owner.
Follow OSHA guidelines for trench safety.
Step 1 Footing Preparation
Excavation is required in most cases to expose
the concrete footing and prepare it for under-
footing bracket placement. The footing may
be accessed from either inside or outside the
structure using isolated “pocket” or continuous
excavations. For structures with basements,
it may be advantageous to access the footing
from within the basement of the structure by first
removing sections of the basement floor slab.
General steps for footing preparation include:
• For shallow pocket excavations, soil should
be hand or machine-excavated from against
the footing and foundation wall within an area
approximately 3 feet square and to a depth
approximately 9 to 13 inches below the bottom
of footing. These excavations are made at
each pier location. Alternatively, soil could be
removed completely with a trench excavation.
Trench excavations are more common when a
lift is required.
• The soil under the footing and foundation wall
is removed to a distance that allows bracket
placement
(Figure 3.10.a)
.
• Notch spread footings 16 to 22 inches wide
(depending upon the width of the retrofit
bracket) and approximately flush with the face
of the foundation wall. Notching of footings may