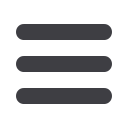
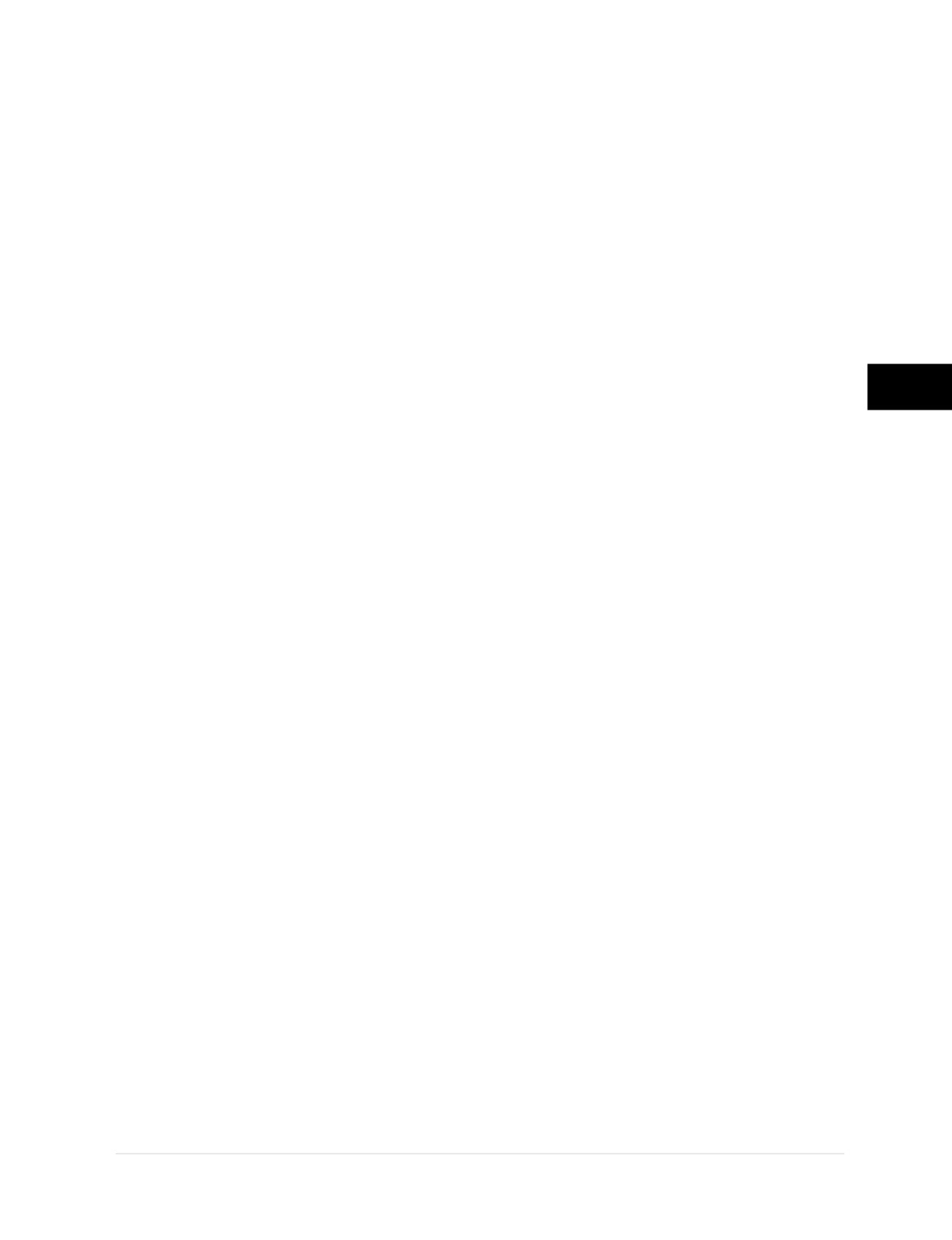
© 2014 Foundation Supportworks
®
,
Inc.
All Rights Reserved
p 235
Chapter 3
Hydraulically-Driven Push Piers
CHAPTER 3
HYDRAULICALLY-DRIVEN PUSH PIERS
capability of unreinforced or under-reinforced
footings, foundation walls and floor slabs, and
not by the pier’s capacity. Monolithic footings,
footings with short stem walls or footings with
masonry stem walls may require closer pier
spacing and/or additional support at the bracket
locations. Spanning capability of a footing may
be improved by using structural steel angles,
plate, tube, etc. sandwiched between the bottom
of the footing and the horizontal bearing plate of
an under-footing bracket. In more severe cases;
e.g., stone, cobble, brick and highly deteriorated
foundations, the footings can be temporarily
undermined in short sections to construct a
continuously reinforced concrete grade beam.
The grade beam would then provide adequate
spanning capability for the installation of the
retrofit piers.
With all the discussion above, a push pier
system can still only provide support for the
structure if competent soils are encountered at
the pier tip. Typically, SPT N-values of 35 to 40
blows per foot for clay soils and 30 to 35 blows
per foot for granular soils are needed to provide
the necessary end bearing resistance for light to
moderate push pier loads. See Appendix 2G for
additional information regarding geotechnical
considerations for push pier systems.
Technical specifications and capacities for FSI
push pier systems are provided in Appendix 3A.
3.9.1 Factor of Safety
The push pier system develops a factor of safety
against pier settlement by the pier installation
methods used and the sequence with which
multiple piers are driven and then re-loaded. Piers
are first driven individually using the maximum
weight of the structure and any contributory soil
load as the reaction. The pier gathers load from
adjacent sections of the foundation, not just in
the immediate area of the pier. The more rigid
the structure, the more load can be transferred
to the pier during the drive process. It is for this
reason, along with consideration of contributory
soil load against the foundation, that piers can
be driven to loads greater than the calculated
service loads.
The drive or installation force on the piers is
determined by calculating the structural load
(dead plus live) and the soil load on each pier,
then multiplying by a factor of safety. Factors of
safety of 1.5 to 2.0 are commonly used for push
pier systems since the drive and lock-off loads
are easily measured and verified using hydraulic
cylinders, pumps and gauges. Foundation
Supportworks does not recommend the use of
bottle jacks for the drive or lift operations of a
push pier installation. Loads applied with bottle
jacks are unknown and not easily determined.
Higher factors of safety may be considered
at the discretion of the project engineer or as
dictated by local codes.
Piers are driven to the calculated “ultimate”
load, or until lift of the structure occurs.
After all of the piers are driven, the piers are
connected in series with hydraulic lift cylinders
and re-loaded to either the design service load
to stabilize the structure, or until the desired
lift is achieved. The total reaction load is then
distributed over the multiple pier locations. The
final factor of safety against pier settlement at
each pier location is calculated by dividing the
drive load by the lock-off load.
As discussed in Section 3.3.2.1, additional
skin friction develops over time as the soils
heal around the pier shaft. The factor of
safety generally increases with an increase in
frictional capacity.
3.9.2 Bolting the Under-Footing
Bracket to the Foundation
Foundation Supportworks does not require nor
recommend bolting of under-footing brackets
to a concrete foundation with expansion or
adhesive anchors. Experience has shown that
bolting to unreinforced or under-reinforced
concrete routinely causes concrete to crack
and spall during installation of the expansion
or adhesive anchors, or during the repeated